Freight Forwarders & Warehousing: Do You Need a WMS?
As warehousing becomes a bigger part of forwarding operations, one question keeps coming up: Do freight forwarders need a WMS?
The answer, increasingly, is yes.
📦 What Is a WMS?
A Warehouse Management System (WMS) is software that helps businesses control and optimize warehouse operations such as:
- Inventory tracking
- Order picking and packing
- Storage location management
- Inbound and outbound shipment control
- Barcode scanning and label generation
- Customer inventory visibility
For freight forwarders, a WMS bridges the gap between transportation and warehousing—offering end-to-end control of goods, whether they’re in motion or at rest.
🔍 Why a WMS Matters for Freight Forwarders
Freight forwarders increasingly act as logistics orchestrators, not just freight handlers. As more shippers request temporary storage, cross-docking, and fulfillment support, warehousing becomes a value-added service—and it needs structure.
Here’s why a WMS matters:
✅ 1. Inventory Accuracy
Avoid losses, confusion, or delays by knowing exactly what’s in your warehouse, where it is, and who it’s for.
✅ 2. Faster Order Turnaround
Improve efficiency in picking, packing, and dispatching freight—critical in high-volume, fast-moving environments.
✅ 3. Streamlined Freight + Storage
A WMS tightly integrates warehouse data with shipping schedules, helping you sync container arrivals with outbound fulfillment.
✅ 4. Transparent Customer Service
Offer clients real-time inventory visibility with personalized dashboards or custom notifications.
✅ 5. Scalability
As you grow, warehouse complexity grows too. A WMS allows you to handle more volume without chaos.
🧭 When Should a Freight Forwarder Use a WMS?
You might need a WMS if:
- You’re offering temporary storage for clients
- You’re running a bonded or multi-client warehouse
- You manage pallets or SKUs per consignee
- You’re picking and packing eCommerce or B2B orders
- Your team manually updates inventory in Excel
- Clients are asking for inventory reports or live updates
If any of these sound familiar, a WMS can save time, reduce errors, and impress customers.
🔧 Linbis WMS: Built for Freight Forwarders
The Linbis WMS is part of the Linbis cloud logistics platform—built specifically for freight forwarders, 3PLs, and logistics providers.
Key Features:
- 📦 Multi-client inventory management
- 📍 Location-based control (racks, zones, pallets)
- 📋 Custom receiving and dispatch forms
- 🔄 Barcode scanning and order fulfillment
- 🌐 Client portal for inventory tracking and reports
- 🚚 Integrated with shipping, billing, and documentation
Whether you’re running a cross-dock, shared warehouse, or bonded facility, Linbis gives you the tools to run warehousing like a pro—without leaving the freight behind.
💡 Real-World Example
A freight forwarder managing air freight for fashion brands integrated Linbis WMS to manage short-term storage between customs clearance and delivery.
Result:
- Reduced inventory discrepancies by 90%
- Cut order processing time by 40%
- Gave clients real-time inventory visibility
- Unified warehouse + shipping ops in one dashboard
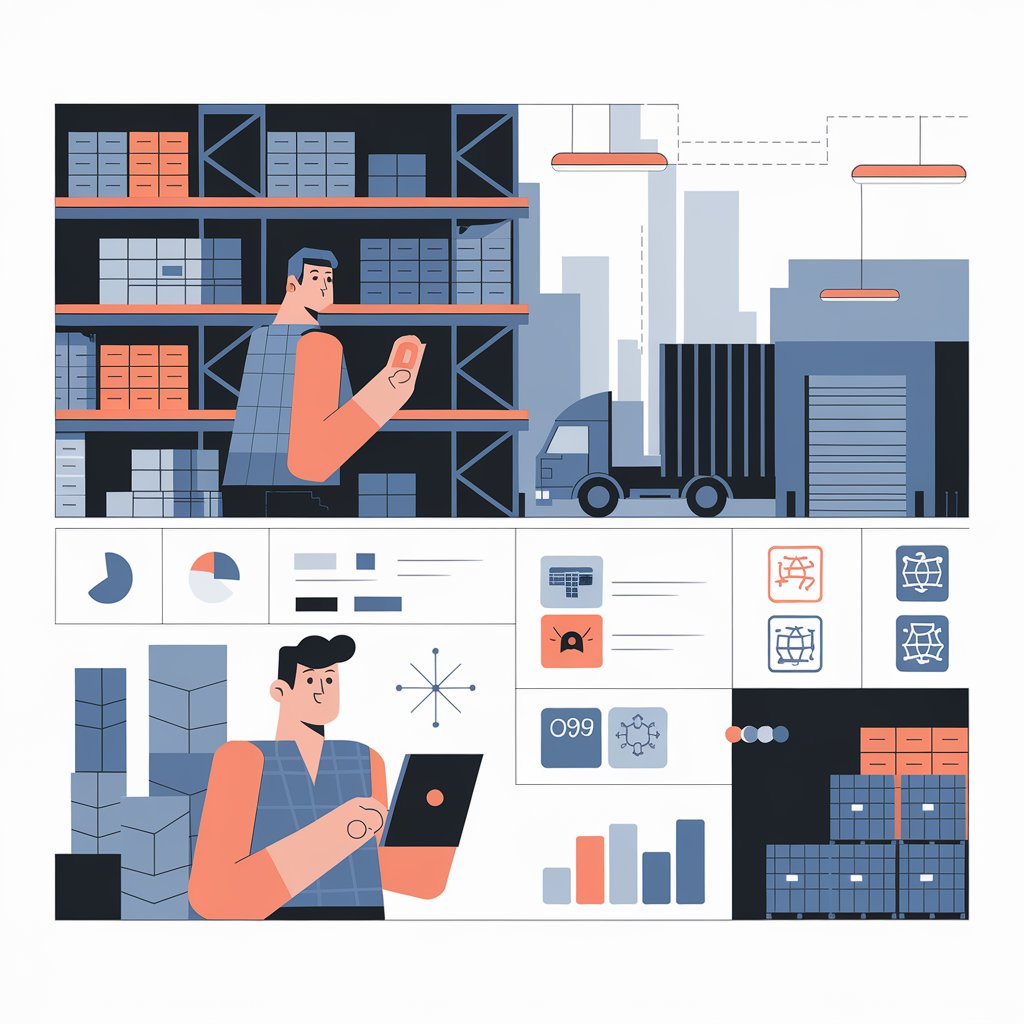
🎯 Final Thoughts
If you’re a freight forwarder and warehousing is becoming part of your value chain, it’s time to move beyond spreadsheets and guesswork.
A Warehouse Management System helps you deliver faster, reduce errors, and offer premium service to clients who expect visibility and precision.
And with cloud-based tools like Linbis WMS, you can get started quickly—without big infrastructure or IT headaches.