Integrating Container Tracking into Your Freight Operations
The real value comes when you integrate container tracking directly into your freight workflows.
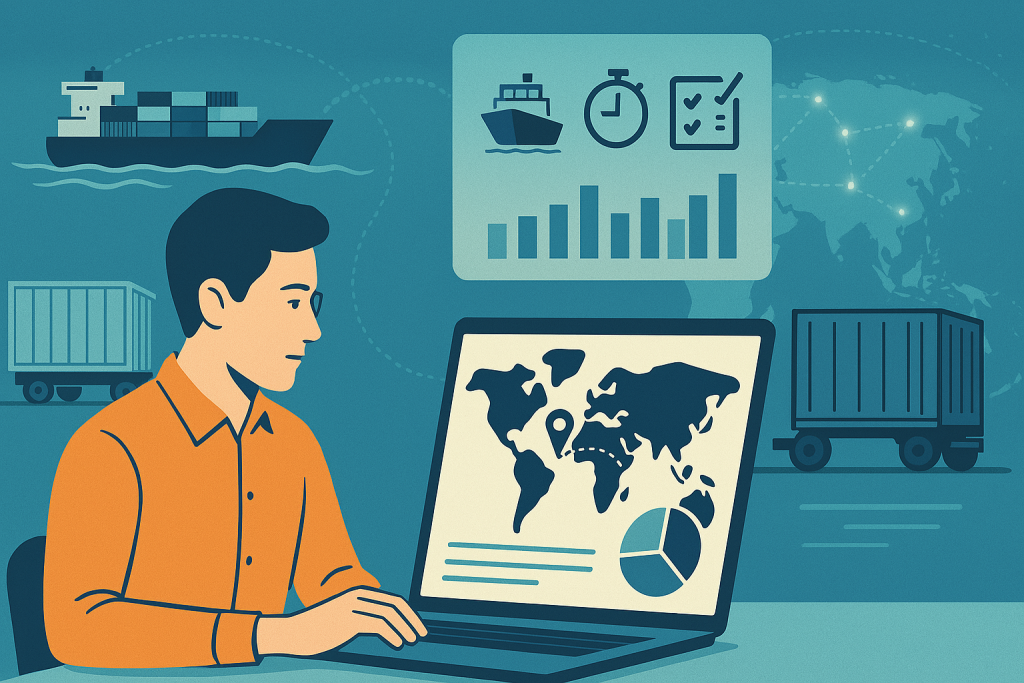
🚛 Why Integrate Container Tracking?
If you’re still copying updates from carrier portals or sending manual status emails, integration will transform your day-to-day operations.
Key Benefits:
- Real-time visibility across your TMS or logistics software
- Automated alerts when containers are delayed or arrive
- Reduced data entry, saving time and avoiding errors
- Improved communication with clients and partners
- Consolidated dashboards for all shipments
Platforms like Linbis make container tracking integration easy with built-in modules and external carrier APIs, so freight forwarders, 3PLs, and shippers can connect tracking to their existing workflows.
🧩 Step-by-Step: How to Integrate Container Tracking into Your Freight Workflow
1. 🧭 Map Your Existing Workflow
Before jumping into tech, understand how your team currently manages containers:
- Where do you enter bookings?
- How are status updates shared?
- What tools do your ops and customer service teams use?
Identify where tracking data would make the biggest impact.
2. 🔍 Choose a Container Tracking System with Integration Options
Look for software that supports:
- API access or integrations with major shipping lines
- Tracking via container number, booking ID, or B/L
- Customizable alerts and shareable links
- Compatibility with your freight platform (TMS, WMS, CRM)
➡️ Linbis, for example, offers container tracking embedded within its freight management system—no need for extra platforms.
3. 🔌 Connect Data Sources
Your tracking platform should pull live updates from:
- Ocean carriers
- Port terminals
- Vessel AIS data
- Customs or port authority systems
This connection should be automatic—no manual updates or copy-paste.
4. 📲 Sync with Operational Tools
Now that your system receives live tracking data, push it into:
- Shipment dashboards
- Customer portals
- Warehouse planning tools
- Client email or SMS notifications
This ensures your team—and your clients—see status updates in real time, where they already work.
5. ⚙️ Automate Alerts & Exceptions
Set triggers to notify teams when:
- A container is discharged
- A delay occurs at transshipment
- Customs clearance is pending
- Final delivery is scheduled
This way, your staff can act proactively, before an issue causes disruption.
6. 📊 Analyze Performance
Integrated tracking doesn’t just improve visibility—it feeds performance data into your system so you can track:
- Average transit times
- Carrier reliability
- Delay patterns by route or port
With platforms like Linbis, this data can be pulled into custom reports or KPI dashboards—giving your team long-term visibility, not just momentary updates.
🔄 Real-World Use Case
A mid-sized freight forwarder integrates container tracking into Linbis. Now they:
- See all container statuses in one dashboard
- Automate delivery alerts to clients
- Coordinate warehouse and drayage based on live ETAs
- Use monthly reports to renegotiate carrier contracts
Result: Fewer surprises, happier customers, and time saved on every shipment.
✅ Final Thoughts
Integrating container tracking isn’t just about tech—it’s about transforming how your team works.
From automation to analytics, integration turns scattered data into seamless workflows that improve planning, reduce friction, and strengthen your supply chain.
If you’re looking to embed container tracking into your freight operations, platforms like Linbis offer flexible tools and integrations that make it easy to scale.